Plastic Thermoforming Process
Thermoforming is a manufacturing process where a plastic sheet is heated to a pliable forming temperature, formed to a specific shape in a mold, and trimmed to create a usable product. It differs from injection molding, blow molding, rotational molding and other forms of processing plastics. Thin-gauge thermoforming is primarily the manufacture of disposable cups, containers, lids, trays, blisters, clamshells, and other products for the food, medical, and general retail industries. Thick-gauge thermoforming includes parts as diverse as vehicle door and dash panels, refrigerator liners and point of purchase displays.
Loading Plastic Materials
The raw plastic thermoforming material comes in sheets or rolls, depending on how thick it is. In general, material thicknesses greater than .080 inches are in sheet form. Since the roll-fed operation is automated, it typically runs faster than sheet form manufacturing. Sheet machines can handle thicker materials, and therefore often make parts that are larger and deeper. PN Products is equipped for both roll and sheet fed manufacturing.
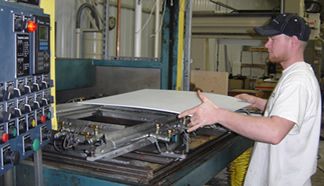
Heating The Plastic Thermoforming Material
The plastic material must be heated to the forming temperature. This temperature varies with the kind of plastic material being used, and the kind of product being made. In general, heat must be applied so the material is uniformly heated throughout, not just hot at the upper or lower surface. The temperature is controlled though the intensity of the heating elements, and the length of time of exposure. When the material is at the forming temperature, you may see it sag a little, as in this picture.
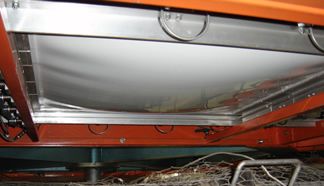
Forming The Heated Plastic
The material is forced against the mold surface, and takes the shape of the mold. If the mold is male, the material is draped over the mold (and forced against it with pressure and/or vacuum). As the material cools, it contracts and sticks tight to the mold. If the mold is female, the material is forced (again by vacuum and/or pressure) into the cavity, and takes the shape of the cavity. If the mold is female, as the material cools, it shrinks away from the mold.
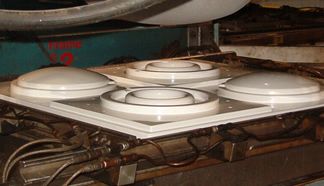
Releasing The Newly Formed Plastic
Once the material has taken the shape of the mold and has been given a little time to stabilize in that shape, it must be separated from the mold. This is generally easier if the tool is female, since the contraction of the plastic material tends to pull it away from the mold. By contrast, contraction forces a tighter fit against a male mold. (This picture shows a male mold.) The release may be assisted by reversing the pressure or vacuum that brought the material and the mold together. The mold cannot have severe undercuts or sharp corners if the release is going to work smoothly and easily.
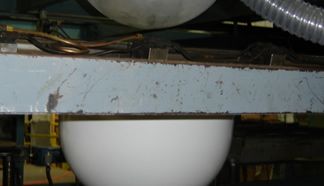
Trimming Excess Plastic Material
Usually there is excess plastic around the shaped part or component, that must be trimmed away. This may be accomplished by sawing, sanding, die cutting, or routing. The method used depends on the size of the part and the requirement for accuracy. PN Products has CNC routing machines for precision trimming, but we also use die cutters and other methods as may be required for efficiency and productivity.
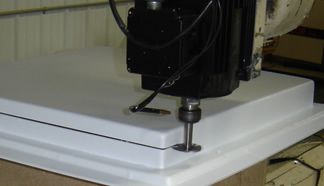
Do you have any questions?
If you are ready to make your project a reality, we’re ready to help. Contact us today to request a quote or learn more about our capabilities.